‘Amphibious’ Sensors Make New, Waterproof Technologies Possible
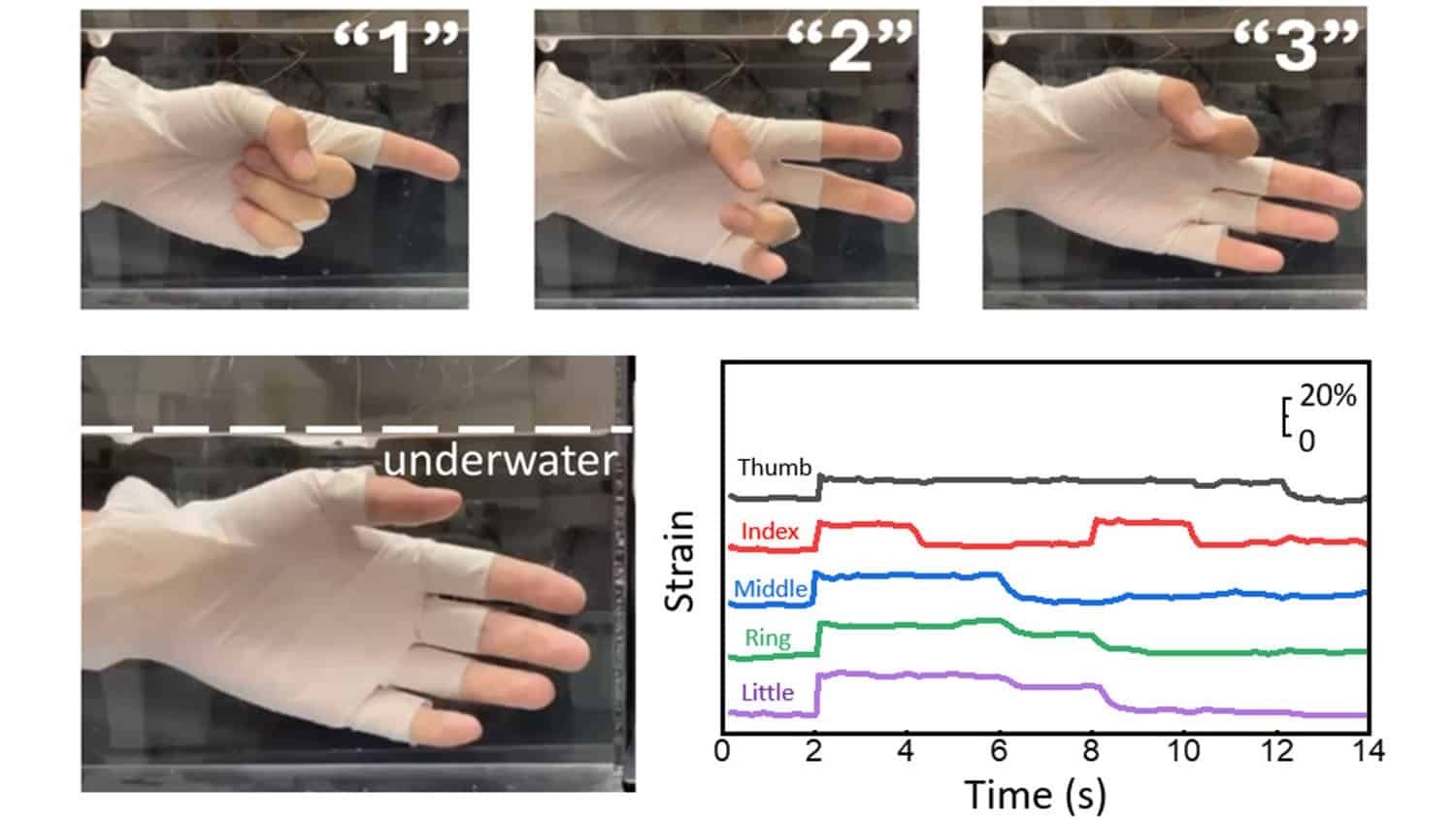
Researchers have demonstrated a technique for creating sensors that can function both in air and underwater. The approach paves the way for “amphibious” sensors with applications ranging from wildlife monitoring to biomedical applications.
The new findings are focused on strain sensors, which measure deformation – meaning they can be used to measure how things stretch, bend and move.
“For example, there is interest in creating strain sensors that can be used in biomedical applications – such as sensors that can be used to observe the behavior of blood vessels and other biological systems,” says Shuang Wu, first author of a paper on the work and a postdoctoral researcher at North Carolina State University. “Other possible applications include creating sensors that can measure how fish move underwater, monitor health in wildlife, and so on.”
“However, a big challenge when creating such wearable or implantable strain sensors is ensuring that the sensors can perform in wet environments,” says Yong Zhu, corresponding author of the paper and the Andrew A. Adams Distinguished Professor of Mechanical and Aerospace Engineering at NC State.
“Our goal with this work was to create sensors that would last a long time in a wet environment without sacrificing the performance of the sensor,” Wu says.
With that goal in mind, the research team began by utilizing a sensitive strain sensor the team developed in late 2022. The researchers then sandwiched the sensor between two thin films made of a highly elastic, waterproof polymer.
The polymer encapsulates the sensor. This keeps water out but does not restrict the movement of the sensor material like most other encapsulations due to its unique interface design. This gives the sensor the desired sensitivity and stretchability. The sensor can be connected to a small chip that transmits data wirelessly.
“In experiments, we found the amphibious sensors were sensitive and had a fast response time,” says Wu. “And we found that the performance of the sensors was the same whether the sensor was in air or after being submerged in saltwater for 20 days.”
“The sensors are also very stable – their performance didn’t drop off, even after being stretched 16,000 times,” says Zhu.
To demonstrate the functionality of the amphibious sensors, the researchers used the sensors to track the motions of robotic fish and monitor blood pressure in a pig’s heart. The researchers also created a glove that incorporated the amphibious sensors, using the sensors to translate a scuba diver’s hand signals into messages that could be read by people in or out of the water.
“The idea was to create an easy way for scuba divers to communicate effectively with other divers underwater or crew members still on a boat,” says Wu. Video of these proof-of-concept tests can be found at https://www.youtube.com/watch?v=nSOB5PTI3j8.
“We’ve submitted a patent application for this technology and are open to working with industry partners to incorporate these sensors into various applications,” says Zhu.
The paper, “Encapsulated Stretchable Amphibious Strain Sensors,” is published open access in the journal Materials Horizons. The paper was co-authored by Doyun Kim, a postdoctoral researcher at NC State; Xiaoqi Tang, a Ph.D. student at NC State; and Martin King, a professor in NC State’s Wilson College of Textiles.
The work was done with support from the National Science Foundation, under grants 2122841 and 2134664; the National Institutes of Health, under grant R01HD108473; and the Department of Defense, under grant W81XWH-21-1-0185.
-shipman-
Note to Editors: The study abstract follows.
“Encapsulated Stretchable Amphibious Strain Sensors”
Authors: Shuang Wu, Doyun Kim, Xiaoqi Tang, Martin W. King and Yong Zhu, North Carolina State University
Published: Aug. 1, Materials Horizons
DOI: 10.1039/D4MH00757C
Abstract: Soft and stretchable strain sensors have found wide applications in health monitoring, motion tracking, and robotic sensing. There is a growing demand for strain sensors in amphibious environments, such as implantable sensors, wearable sensors for swimmers/divers, and underwater robotic sensors. However, developing a sensitive, stretchable, and robust amphibious strain sensor remains challenging. This work presents an encapsulated stretchable amphibious strain sensor. The conductive layer, made of silver nanowires embedded below the surface of polydimethylsiloxane, was sandwiched by two layers of thermoplastic polyurethane. Periodic sharp cuts were introduced to change the direction of flow from across the sensor to along the conductive path defined by the opening cracks. The crack advancing and opening is controlled by a unique combination of weak/strong interfaces within the sandwich structure. The cut design and the interfacial interactions between the layers were investigated. The strain sensor exhibited a high gauge factor up to 289, a linear sensing response, a fast response time (53 ms), excellent robustness against over-strain, and stability after 16?000 loading cycles and 20 days in an aqueous saline solution. The functionality of this amphibious strain sensor was demonstrated by tracking the motion of a robotic fish, undertaking language recognition underwater, and monitoring the blood pressure of a porcine aorta. This illustrates the promising potential for this strain sensor for both underwater use and surgically implantable applications.
This post was originally published in NC State News.