Technique Speeds Up Thermal Actuation for Soft Robotics
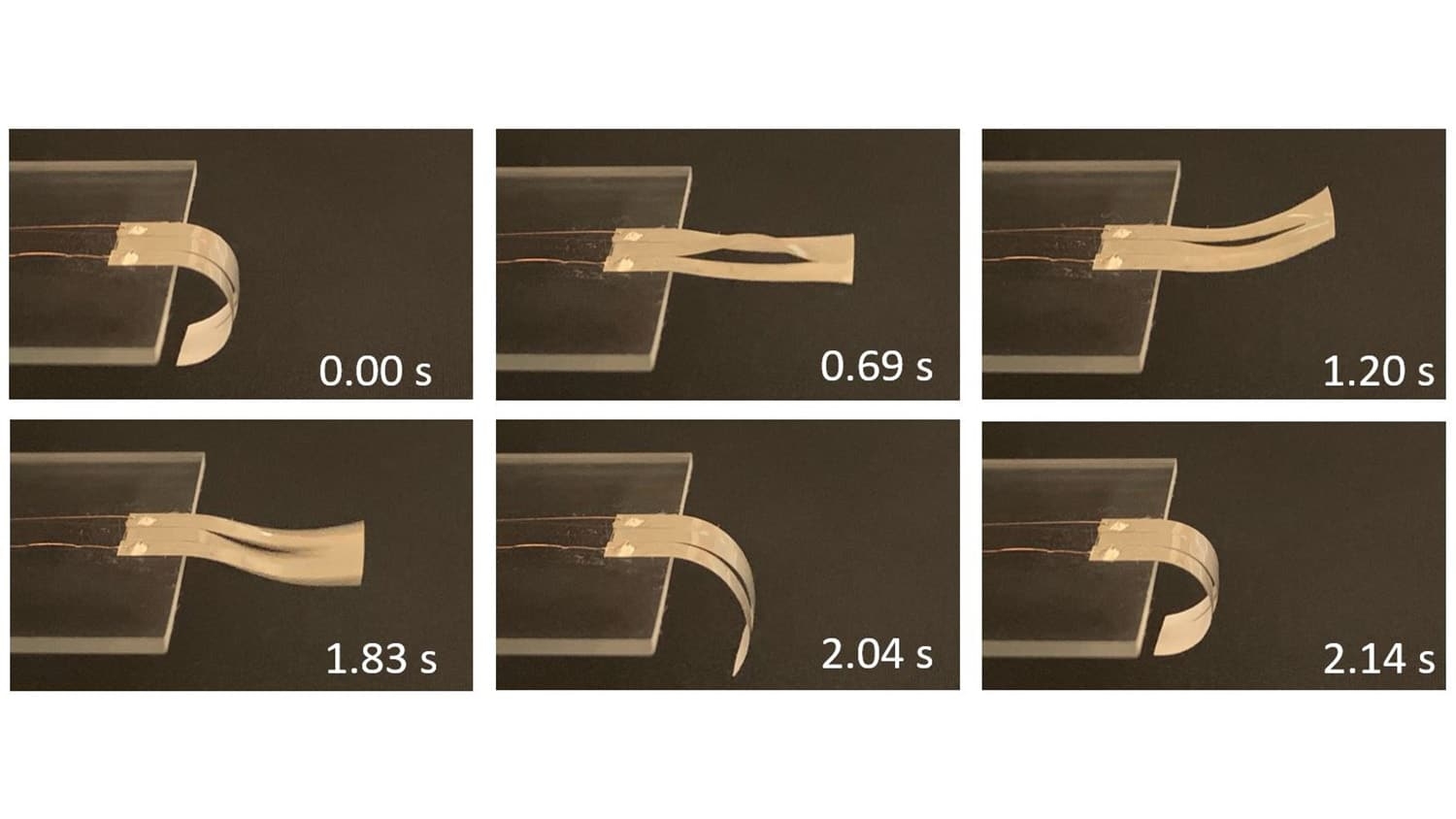
Researchers from North Carolina State University have come up with a new design for thermal actuators, which can be used to create rapid movement in soft robotic devices.
“Using thermal actuation is not new for soft robots, but the biggest challenge for soft thermal actuators was that they were relatively slow – and we’ve made them fast,” says Yong Zhu, corresponding author of the paper and the Andrew A. Adams Distinguished Professor of Mechanical and Aerospace Engineering at NC State.
Actuators are the parts of a device – such as a soft robot – that create motion by converting energy into work.
“What makes this new actuator design work is a structure with a bi-stable design,” says Shuang Wu, first author of the paper and a Ph.D. student at NC State. “Think of a snap hair clip. It’s stable until you apply a certain amount of energy (by bending it over), and then it snaps into a different shape – which is also stable.”
In the case of the new thermal actuator, the material is bi-stable, but which shape the material prefers is dictated by temperature.
Here’s how that works. The researchers layer two materials on top of each other, with silver nanowires in the middle. The two materials have different coefficients of thermal expansion, which means they expand at different rates as they heat up. In practical terms, that means the structure bends when you heat it.
This layered material is then shaped into a design that gives it a default curvature in one direction – let’s say that it curves downward. When voltage is applied to the silver nanowires, the material heats up, making it bend in the other direction. Once you reach a certain temperature – the critical temperature – the material snaps into its new default shape, curving up rapidly. When the voltage is removed, the temperature goes back down. Once it cools past another critical temperature, the material snaps back to its previous default shape, curving down rapidly. Note that the two critical temperatures are different; the first one is higher. By applying current to the nanowires in a regular pattern, you can make the material snap back and forth.
To demonstrate the technique, the researchers created two prototypes. One of the prototypes emulates the snapping behavior of a Venus flytrap, while the other is a “crawler” capable of moving more than one body length per second.
“Potential applications range from biomedical applications to prosthetic devices to high-end manufacturing,” Zhu says. “Any application in which you’d want to be able to move quickly, but also want to avoid rigid materials and conventional robotics.”
Next steps include developing sensor and control mechanisms that could more fully automate the actuation process, allowing it to operate more efficiently than purely manual controls.
“We’re also interested in exploring other possible materials, so that we could fine-tune the thermal and mechanical properties,” Zhu says. “This could allow us to tailor both actuator speed and force.”
The paper, “Fast Thermal Actuators for Soft Robotics,” is published in the journal Soft Robotics. The paper was co-authored by Langston Baker, a former graduate student at NC State; and Jie Yin, an associate professor of mechanical and aerospace engineering at NC State. The work was done with support from the National Science Foundation, under grant number 1637892.
-shipman-
Note to Editors: The study abstract follows.
“Fast Thermal Actuators for Soft Robotics”
Authors: Shuang Wu, G. Langston Baker, Jie Yin, Yong Zhu, North Carolina State University
Published: Dec. 7, Soft Robotics
DOI: 10.1089/soro.2021.0080
Abstract: Thermal actuation is a commonly used actuation method for soft robots. However, a major limitation is the relatively slow actuation speed. Here we report significant increase in the actuation speed of a bimorph thermal actuator by harnessing the snap-through instability. The actuator is made of silver nanowire/polydimethylsiloxane composite. The snap-through instability is enabled by simply applying an offset displacement to part of the actuator structure. The effects of thermal conductivity of the composite, offset displacement, and actuation frequency on the actuator speed are investigated using both experiments and finite element analysis. The actuator yields a bending speed as high as 28.7 cm-1/s, 10 times that without the snap-through instability. A fast crawling robot with locomotion speed of 1.04 body length per second and a biomimetic Venus flytrap were demonstrated to illustrate the promising potential of the fast bimorph thermal actuators for soft robotic applications.
This post was originally published in NC State News.